Volker bygger en egen CNC-fräs
2021-08-23
Inget handhållet verktyg är lika exakt. Många skulle därför gärna vilja ha något annat som de kan göra måttillverkat av trä eller metall med – en CNC-fräs. Volker har byggt sig en egen. På en workshop – för det är knappast möjligt utan professionell hjälp.
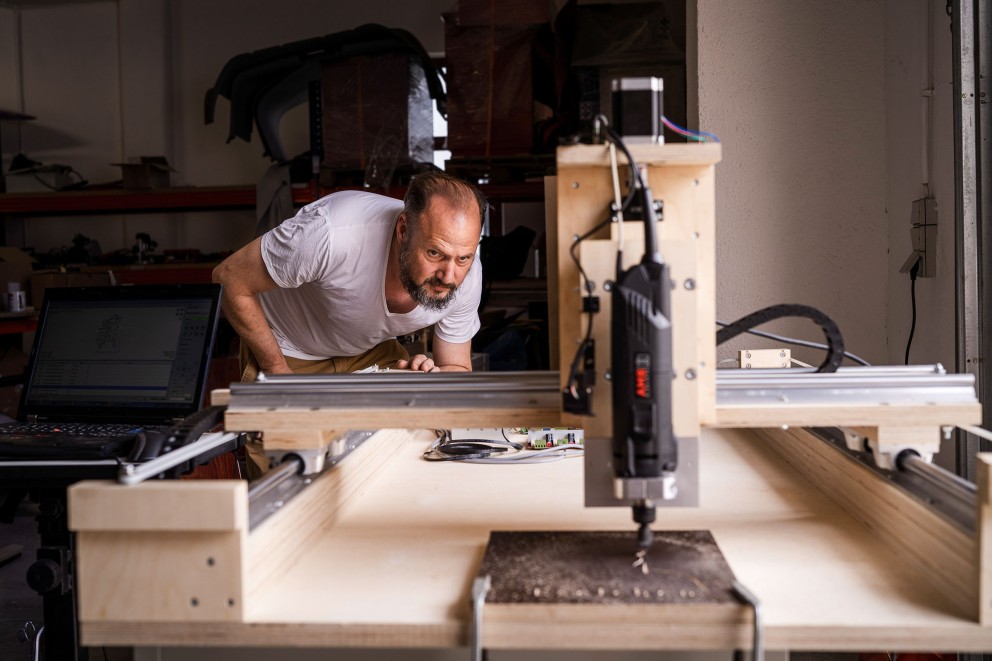
När jag skulle börja kände jag framför allt stor respekt inför uppgiften. Och för själva maskinen – CNC-fräsen! Bara namnet låter komplext, precist och proffsigt, näst efter verktyg och dator, hårdvara och mjukvara. CNC står för ”Computer Numerical Control”, vilket alltså innebär en digitalt styrd fräs. Utan sådana fräsar fungerar egentligen ingenting inom tillverkningsindustrin i dag. Inte inom vare sig metallbearbetning eller möbelbranschen. Framför allt när det gäller större tillverkningsvolymer. Vad CNC-fräsen i slutändan ska bearbeta för något – trä, aluminium eller plast – är upp till operatören. När all data väl har matats in är det programmet som styr maskinen och bestämmer varvtal, matning och skärdjup. I den professionella versionen kostar en sådan fräs lätt 100 000 euro (drygt 1 miljon svenska kronor), men det finns också versioner för gör-det-självaren. Av en ren tillfällighet fick jag veta att man relativt billigt även kan bygga en själv. På en workshop, som till exempel den som Birgit Hellendahl håller. Jag har till exempel alltid velat bygga mina egna möbler, exakt utfrästa. Perfekt, tänkte jag. Det ska jag göra.
Text: Volker Corsten | Foto: Sebastian Berger